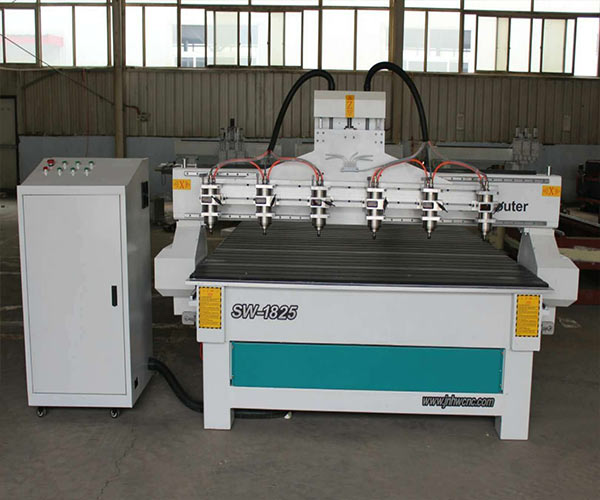
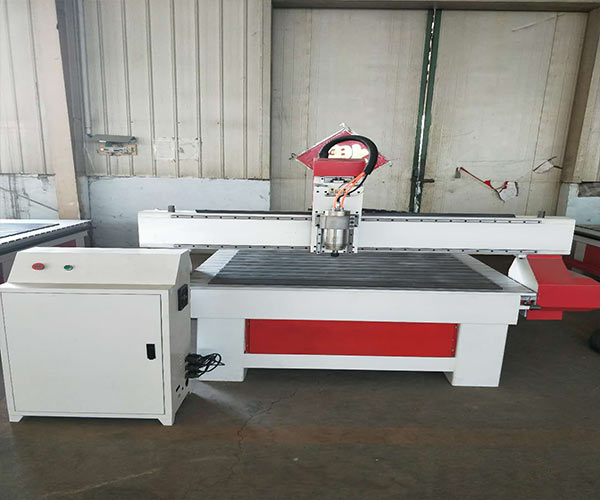
The following precautions should be taken when cleaning the vibration engraving machine:
1. Ensure that the device is turned off and the power is disconnected.
2. Use a soft cloth, sponge, or brush for cleaning, avoiding rough materials or metal tools to prevent surface damage. Do not pour any liquid directly onto the motor or other sensitive components to prevent short circuits. The standard equipment of the machine can be used to clean accumulated impurities such as dust and small particles.
3. For sliding parts (such as blade slider), lubricant should be applied to keep them smooth. Don't forget to remove any remaining graphite powder and other small fragments that may remain in every corner to avoid malfunctions caused by stone inclusions.
4. Regularly check if all fasteners are securely locked to prevent hard foreign objects from falling and damaging the components and mating surfaces of the entire machine; Pay attention to protecting the lenses on the body from scratches. The lenses can be wiped and gently treated with dust-free paper; Before each operation, turn on the machine and adjust the parameters (if the order is reversed, there is a risk of burning the board); It is strictly prohibited to touch the running drum body and stopper rod during the processing. If any abnormalities are found, they should be promptly repaired and contacted with maintenance personnel to ensure safe and error free production. During cutting, efforts should be made to ensure that the amplitude, frequency, and spindle speed are controlled reasonably without deviating from the center trajectory; The replacement of graphite sheets should be standardized, timely, and accurately installed with screws and anti loosening washers to ensure normal operation. In addition, it is necessary to regularly clean and maintain good hygiene of the aircraft body and its surrounding areas, so as not to leave any chance for dust to fall to the ground, and not to ignore some inconspicuous floating dust as a small matter. Only by doing a good job in equipment maintenance and using it correctly can we extend its service life, reduce losses, save costs, and create greater benefits rather than a one-time solution. In order not to affect work efficiency, attention should also be paid to daily preventive measures to lay a good foundation for subsequent safety production!!
5. It is recommended to use a central vacuum pump with water absorption function to blow dry the coolant, which can better absorb moisture and improve the drying effect, so that internal parts will not rust or corrode due to moisture erosion..