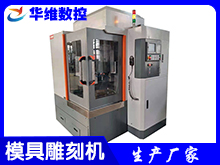
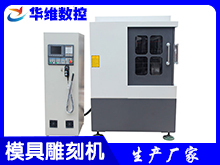
The operation process of the automobile mold machine is as follows:
1. Confirm the processing content, understand the part drawings and process requirements that need to be made. Adjust the machine according to the drawings and on-site conditions. Check if the spindle has reached the required temperature range (generally controlled between 40 ℃~65 ℃, not exceeding 72 ℃). Perform functional testing on each component of the equipment before trial molding or production; Ensuring the integrity and stable operation of equipment is one of the crucial work processes. Prepare the necessary tools and fixtures, and prepare the steel plate for cutting (this process should be labeled with material numbers so that it can be restored to its original shape during maintenance). If conditions permit, computer-aided manufacturing systems (CAM) can also be used to improve accuracy and efficiency, as well as the required quantity. Simultaneously set the required material parameters and input the hardness value of the material to control important data such as extrusion force during molding and cooling time for final molding. The adjustable range of cold stamping steel is generally from 3mm to 8MM thickness, which can be adjusted to meet the different characteristics of different types of plates you need to meet different needs. At the same time, it should be noted that the new machine can only be put into production after the no-load test is normal to reduce the probability of failure and ensure work efficiency and maintain the performance and safety of the machine tool
It should be noted that the workpiece clamping must be correct, stable, and reliable to prevent deformation, ensuring the sharpness of the convex and concave die cutting edges and improving their service life; And strictly adhere to the requirements of cutting parameters to improve product quality, save raw materials, and reduce costs; In addition, CNC blades with problems should be replaced in a timely manner to avoid affecting the product qualification rate and delivery time, and wasting the consumption of raw materials. It is also necessary to fulfill the important role of cleaning and maintaining the cleanliness of the workshop, without neglecting any small garbage, to ensure the health of personnel, protect the physical and mental health of employees, and add luster to the corporate image! Due to the use of automatic loading and unloading devices in large batches, not only is it labor-saving, but it can also achieve the function of fixed length cutting, greatly improving labor productivity, reducing labor costs, and minimizing unplanned expenses for enterprises, ensuring safety production and promoting the continuous improvement of modern management level of enterprises. We also need to pay attention to the tracking and timely feedback of finished product quality. For some special specifications of products, we should flexibly arrange for production and post-processing according to user needs, and try to win back customers and expand market share for the sake of users. At the same time, we should also improve interpersonal relationships, enhance personal qualities, and establish good moral character! After completing these steps, you can proceed to the next round of learning and training that combines theory and practice, summarize experiences and lessons, and continuously improve yourself to become a qualified mechanical engineer!.
The above are only basic operating procedures, and actual operations may vary depending on specific work environments and requirements. It is recommended to refer to the relevant instructions or training received before carrying out specific operations.