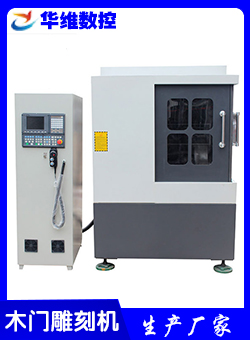
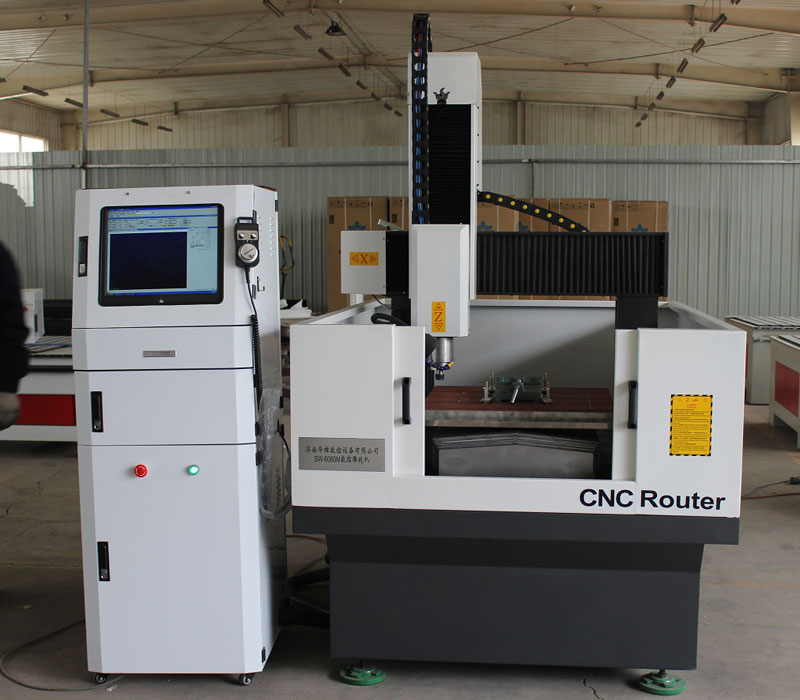
The machining process of automotive molds can be divided into the following steps:
1. Determine the shape and size of the blank according to the design drawings and carry out relevant processing.
2. Perform rough turning to remove a large amount of excess material to a diameter of approximately 50mm. In the process of heat treatment for convex and concave molds, after changing the model and heating, the hardness of the raw material can be basically reached (carburizing is greater than 43HRC). Considering the installation arc radius and the working force situation, the material is generally one to two grades larger than the punch.
*The selection of machine tools such as rocker drills or gantry planers depends on the size of the parts to determine the appropriate equipment. The design requirements for the fixtures and jigs are to ensure that the R angle that conforms to the drawing is finely ground, while also providing an angle forming tool head structure that is easy to operate and maintain. It is important to control the ratio of spindle speed and feed rate during the cutting process to ensure that the tool electrode accuracy meets quality requirements. In special cases, CNC milling machines or other supporting machine tools such as carving and milling machines and mirror spark machines may be used. Factories may directly use cutting tools for manual repair, which has relatively low efficiency and high cost, but a high pass rate can ensure high-precision forming. And during the repair process, the polished metal powder will be collected and processed by a magnetic polishing machine to restore its original rigidity and prevent stress cracking in the later stage; The process solution of using copper materials to remove stress through the combination of pliers and firing can also be supplemented by local small angle blade breakage, excavation and correction, and the above-mentioned grinding and chamfering CNC contour imitation composite processing; One of the characteristics of non-standard parts production is that there are many ways of such defects.
The total time of the entire process may exceed an hour or even several hours to complete a product, so a patient and meticulous operation process is needed to ensure the final quality effect. In addition, it is necessary to pay attention to safety issues and strictly comply with relevant regulations and technical standards for job management.