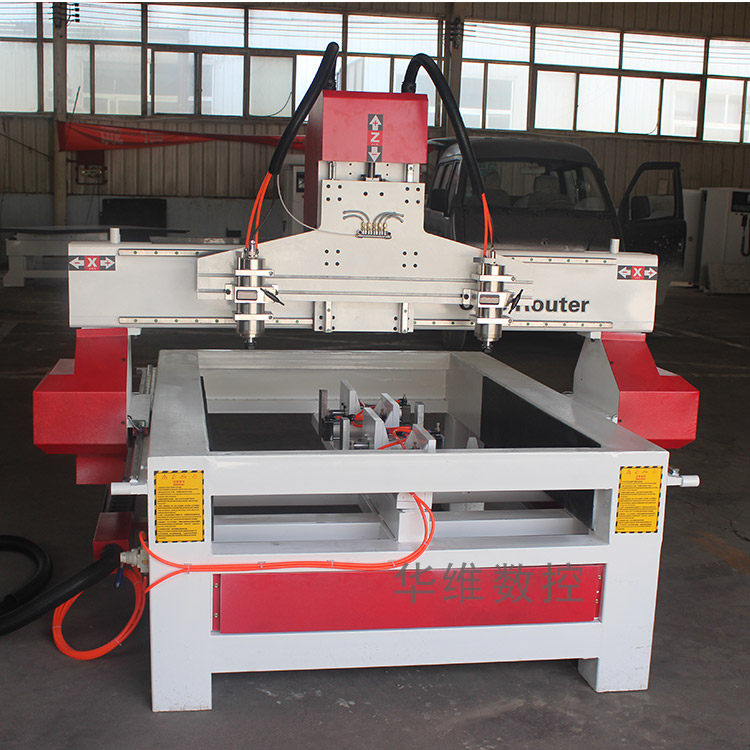
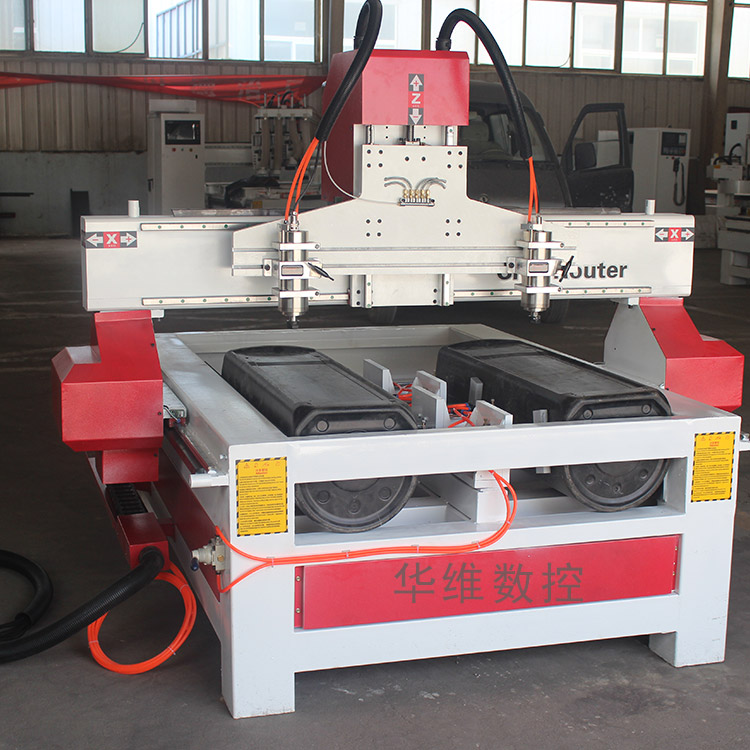
The common faults and solutions of laser cutting machines are as follows:
1. The operating software reports errors or has no response. Perhaps due to incorrect parameter settings, it is necessary to check and adjust the relevant parameters. Incorrect letter variables can also cause this problem; Inappropriate setting of overload protection switch may also cause this situation to occur. The problem can be solved by readjusting the current limiting resistor of the amplifier module tube angle; There is an error in the program flow of the main control computer. You can try turning on the control power to restart the machine (waiting for a short period of strong noise), or restoring the factory settings for initialization processing, adjusting various values according to the actual situation, and conducting processing tests to troubleshoot and repair the corresponding problems. (Generally speaking, it is not recommended for individuals to disassemble and repair at will). It is also recommended to regularly maintain and upkeep the various components of the equipment to ensure that they are in good working condition and extend their service life~
2. Damage to the guide rail, including pulling and crawling towards the edge of the blade holder, may affect the operational efficiency and performance of the equipment; This type of damage is usually caused by irregularly changing light bands. These can be alleviated by adding lubricants and oiling them. At the same time, for the light guide wheels that we often use, we also need to pay attention to their wear level and replace them in a timely manner to avoid affecting our use effect, and so on! Afterwards, it is necessary to pay attention to daily cleaning of dust and impurities to avoid unexpected situations.
3. The reasons for the problem of no pulse output are generally due to poor contact of the high-frequency power controller, which causes the continuous discharge potential to be uneven, resulting in the "stuck" phenomenon where its sensing position cannot return to the origin, or due to large voltage fluctuations. Therefore, we need to debug and maintain it to solve this problem. The above content is for reference only, and the specific solution needs to be determined based on the actual problem and brand/model. If you have any questions, you can consult the after-sales personnel for on-site inspection and handling.. I hope the above information can be helpful to you (≥ ▽≤). Of course, you can also obtain more relevant information by viewing the published documents and other means ☆△ ● In short, when encountering any problems, don't be too anxious and stay calm and rational to analyze and find solutions (* ^ ω ^ *)